Freight cost visibility limitations
Our client is a 100% New Zealand owned and operated wholesaler with a 100 year history of delivering fresh and frozen produce throughout NZ. They have a large number of customer orders and a significant large cold chain component of deliveries.
Our client needed to address inefficient picking, staging and dispatch processes that limited accessibility to the benefits of right-sizing vehicles and fleets.
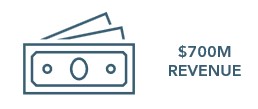
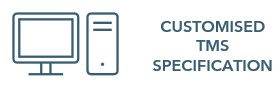
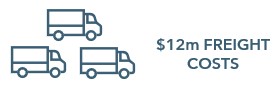
Design, engage and implement
Prological was engaged to:
- develop a detailed understanding of the current operations
- design the freight tasks and supporting processes as required by the client and their customers
- evaluate Transport Management System (TMS) solutions against a clear, operationally-defined requirements specification.
National cost reduction opportunities
Prological identified best practice transport management opportunities including:
- a reduction in the number of trucks and drivers at some stores; a reduction in the size of certain vehicles at most stores without compromising service
- a TMS specification aligned with our client’s safety, compliance, service, control and cost service delivery requirements.