Warehousing dangerous, non-compatible products and explosives
Our client, a commercial explosives and blasting systems manufacturer with revenue of $5b, identified a requirement to relocate one of their mining support facilities from a specifically designed facility to an old and smaller company-owned warehouse in a different location.
The second site had to be repurposed to accommodate the profile of dangerous goods, including non-compatibles product and explosives.
Design requirements included a large temperature-controlled zone (2-8°C), captive cleaning areas, loading and unloading docks, internal and external work areas and goods storage. All options were to comply with LGA, State Government and ADG V7.1 requirements as well as the client’s safety standards.
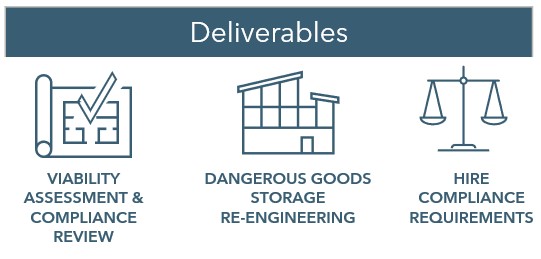
Viability and regulatory compliance assessments
Phase one involved a viability assessment and compliance review. Viability was established, although this was subject to a specific set of conditions, building modifications and inventory profiling.
Three designs were developed, each with different value propositions. These designs were then scrutinised by the regulatory bodies resulting in a set of criteria relating to implementation.
Design concepts and processes meet compliance
All compliance conditions were met and the project was completed in approximately 16 weeks.
The solution combined elements of two design concepts including a 2-8°C temperature-controlled zone. New processes for product bundling and separation and outdoor captive cleaning were also implemented.